Grants related:
The Integration and Mechanical Verification Laboratory, managed by the Mechanics Department, provides the basic and specific infrastructures necessary for the assembly, integration and verification of the medium-sized mechanical systems that are developed in the Instrumentation Area. This laboratory has an area of 42 m2 conditioned to work with mechanical devices and systems, containing a variety of general purpose measurement and test equipment, and with the usual infrastructures of a R&D laboratory. It has air conditioning, compressed air, computer network, three-phase, single-phase and uninterrupted power supply, telephone network, access control system, security systems, etc. In this laboratory there are several specific elements for integration, measurement and mechanical verification, such as gauges, cryostats, vacuum pumps, temperature and pressure data acquisition systems, torque meters, submicron measuring equipment, vibration measurement and analysis equipment, etc. And, as auxiliary infrastructure, it also has multiple mechanical tools, workbenches, shelves, storage trolleys and manipulation elements.
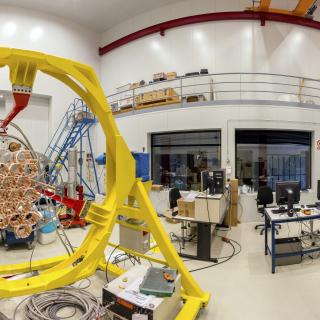
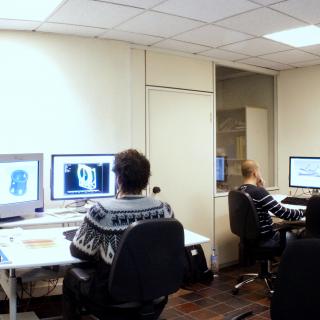
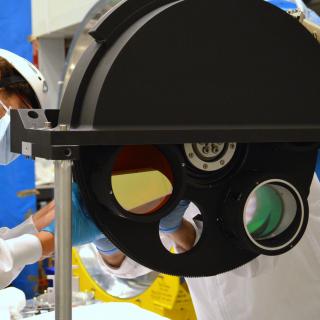
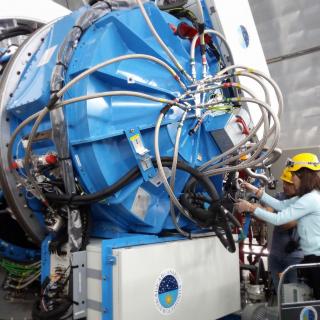